Industrial gaskets perform simple, but critical functions in many industries. Though most gaskets are relatively low cost, they are not necessarily interchangeable between applications. Choosing the right material can impact the gasket’s performance and longevity, ultimately reducing maintenance, replacement, and downtime costs. Silicone is a common high-performance material used for various applications, but an ethylene propylene diene monomer (EPDM) gasket is often a superior choice for specific situations.
Properties and Applications of EPDM and Silicone Rubber
Silicone and EPDM each have value in specific applications. Understanding the properties and capabilities of each material will help to ensure selection of the best material for the job.
. Silicone Rubber

Silicone rubber is a high-performance polymer consisting of carbon, hydrogen, oxygen, and silicone. Silicone rubber is known for its exceptional resistance to extremely high and low temperatures. The material offers additional benefits for gaskets because of its excellent tensile strength, elongation, tear strength, and compression set. Silicone also provides outstanding resistance to chemicals, ozone, water, fire, and aging.
Additionally, silicone rubber is resistant to fungal growth and is considered a sterile material suitable for use in the food and beverage industry. Silicone rubber gaskets have a long life span, which means savings on replacement costs and less equipment downtime. The versatility of silicone rubber makes it ideal for a broad range of applications, and it is used extensively across many industries.
. EPDM
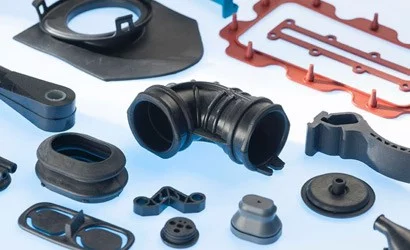
EPDM is created by adjusting the proportions of ethylene and propylene when manufacturing solid polymers like polyethylene and polypropylene. By controlling the polymerization process and regulating the formulation, long molecular chains are created, enhancing EPDM’s rubbery characteristics.
The material’s tensile strength is higher than silicone and most other polymers, and it is highly resistant to abrasion. EPDM is a very stable material that can be formulated to remain flexible at extreme temperatures. It also features excellent resistance to heat and oxidation and withstands the effects of ozone and UV rays. While oils and petroleum products cause EPDM to swell, the material has excellent steam resistance and resistance to nearly all acids and alkalis.
EPDM’s ability to function at low temperatures and its resistance to water, sunlight, and harsh weather conditions, make it ideal for many outdoor gasket applications. Its good compression set enables it to recover well in applications where a joint may open up occasionally, and its high electrical resistance makes it suitable for some electrical applications.
Temperature Resistance | Tear Resistance | Stretchiness | Ozone/UV Resistance | |
EPDM | +130 °C to -40 °C | Good | Good | Excellent |
Silicone Rubber | +230 °C to -60 °C | Excellent | Excellent | Excellent |
Choosing the Right Material for Your Gasket
While gaskets are a relatively inexpensive component, choosing the right gasket material for your application is critical. Gasket failures often occur due to the wrong choice of material for the environment. When deciding whether to choose silicone rubber or EPDM as a gasket material, many factors must be considered, including:
- Temperature
- Abrasion
- Chemical, UV, and ozone resistance
- Pressure considerations
- Electromagnetic interference
Get More Information on Gasket Materials
At ANGOF, our team of engineers and experts consult with you to understand your unique application’s needs. With intimate knowledge of your requirements, our team can provide the expertise needed to choose the gasket material that will offer the greatest lifespan and minimize equipment downtime.
Our Guide to Gasket Material Selections will help you understand the differences in gasket materials. For other questions or help selecting a gasket material for your application, contact us or request a quote today to info@angoindustry.com